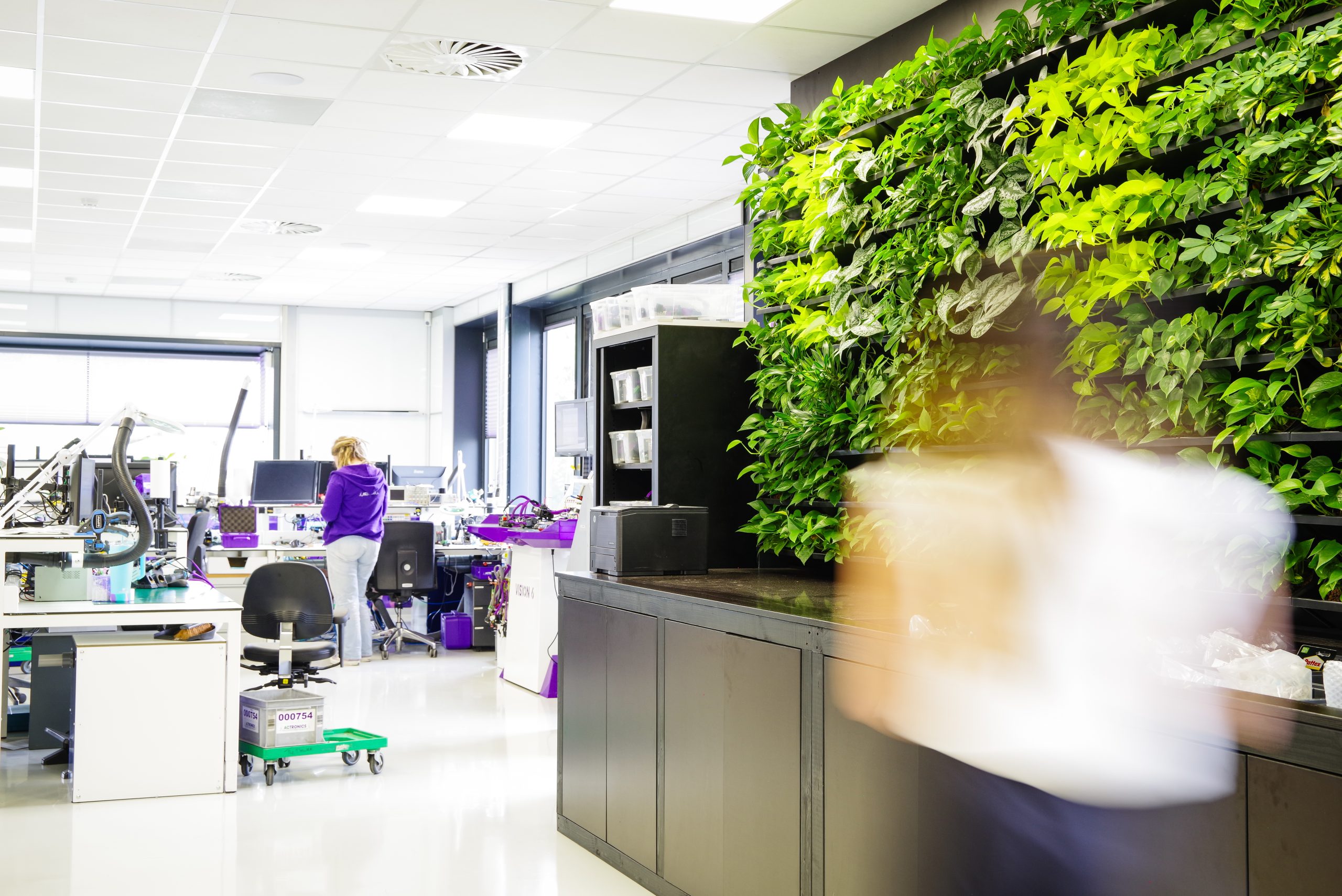
Our Ambitions
Our role within the circular economy
Worldwide, mountains of waste continue to grow, our raw materials are running out and large amounts of CO2 is being released into the atmosphere. We feel a distinct responsibility to contribute as much as we can to a circular world. Within the automotive industry, there are big steps being taken to reduce waste, minimise raw material consumption and to limit CO2 emissions.
ACTRONICS wants to precent products from ending up in landfill and strives to offer circular solutions that are both affordable and attractive. That is why we at ACTRONICS have been giving new life to automotive electronics for over 20 years.
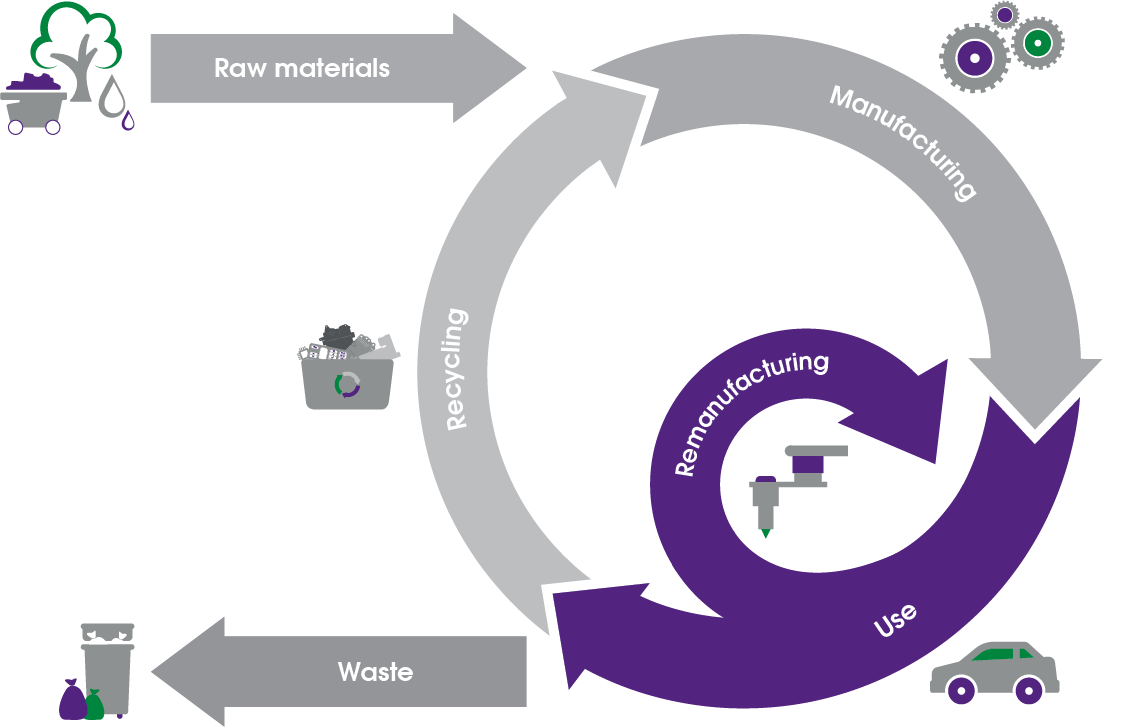
ACTRONICS has saved over 100,000KGs of raw materials
That is equivalent to:
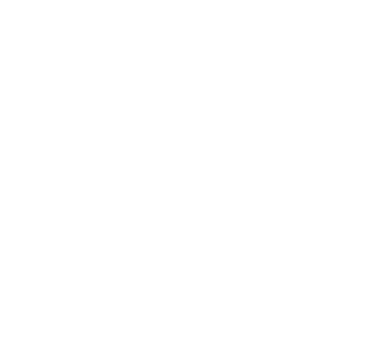
80 cars
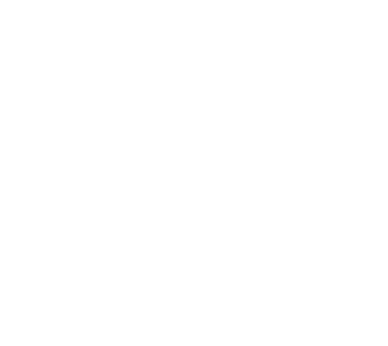
4000 bicycles
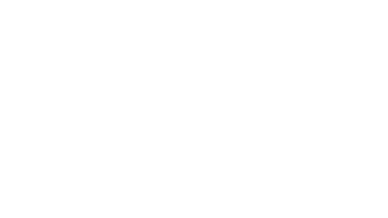
1.750.000 tennis balls
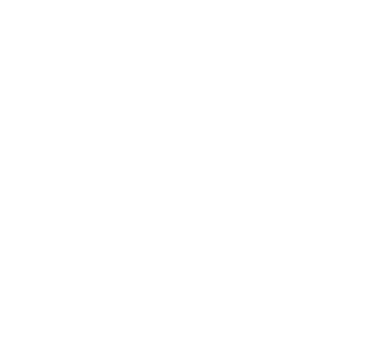
1 space shuttle
Circular company by 2040
Our goal is to be a fully circular company by 2040. An ambitious but beautiful goal! This means that we not only remanufacture electronic components, but also reuse, recover or recycle our own materials. In doing so, we can close the circle from raw materials to finished product.
Some concrete steps we’re already taking:
- An internal recycling program through which we recover materials such as metals, plastics and electronics.
- Encouraging internal reuse, from office supplies to overhaul equipment and parts to reduce our own waste.
- Making not only our customers but also the community aware of the sustainable benefits of remanufacturing compared to the traditional replacement.
Focus on EV Remanufacturing
Our goal is playing a leading part in extending the lifetime of EVs. EVs play a crucial role in the transition to a more sustainable mobility landscape and justify a strong focus. We are therefore continuously expanding our expertise in remanufacturing solutions for Electric Vehicles.
The steps we’re already taking:
- Setting up an R&D team focussed squarely on the future needs of the EV market and continuously researching new repair techniques.
- Investing and developing remanufacturing technologies for various EV models.
- Employees attend training course on the latest EV technologies and overhaul procedures.
Reducing emissions through material
Our goal is to constantly reduce our carbon footprint. To achieve this, we choose sustainable materials, optimised packaging and reusable systems. We also proactively purchase defective products and parts for remanufacture.
After remanufacturing them, we can deliver these products directly from stock. On the one hand, this enables us to reduce a waste stream that was previously beyond our control, on the other hand, we speed up our service considerably by being able to deliver from our own stock.
Some concrete steps we are already taking:
- Expanding our remanufacturing program to buy defective parts in advance, remanufacture them and manage them as stock.
- Optimising our internal logistics process.
- Using new packaging materials, such as reusable boxes for returning remanufactured products to our customers.
Reduced operational emissions
Our goal is to reduce operational emissions by 2030. In doing so, we focus on emissions from every source within our business operations. These include our production facilities, company vehicles, business travel, commuting, waste and discarded components.
The steps we’re already taking:
- All our employees have free access to our charging stations for cars and bikes.
- We reduce waste by using sustainable materials, separating waste and providing everyone with their own reusable water bottles, cups and clothing.
Our Impact
We want to maximise our impact on the 4 Rs. This means we are committed to reducing waste, reusing materials and renewing our processes through innovative techniques. These principles are our guiding principles.
Reuse
We give faulty parts a new lease on life. Faulty car electronics are not just thrown away; we remanufacture these parts to repurpose them and contribute to a more sustainable car industry. If a workshop opts for a new part, we ask them to send us the defective parts. Often, we can stil recondition these parts or reuse them in some other way. We supply such remanufactured parts from stock. Our reuse method further helps to minimise the amount of waste produced by our industry.
Reduce
Reduced waste through remanufacturing. Our core bueinss focues on reducing waste from automotive electronic components. We work on a variety of parts from small components such as ECUs weighing less than 1kg to larger onboard chargers which can weigh more than 15kg. By remanufacturing these components, we minimise the material waste and reduce the need to produce new parts.
Recycle
Responsible recycling if reuse is not viable. If reuse is not an option, we provide responsible recycling of car electronics. This means that we separate and process materials such as the defective parts and metals, in a way that minimises the environmental impact.
Renew
Innovative remanufacturing techniques for sustainable reuse. We continuously develop new techniques to improve the functionality and efficiency of automotive electronics. When renewing parts during remanufacture, we thoroughly address all weak points, not just defective parts.
Thus, we strive to return our remanufactured products to a better than new state, resulting in a higher quality and longer lasting product.
Circular Economy Partner
Since 2016, ACTRONICS has been a proud partner of Circle Economy, a collaboration that underlines our commitment to a circular economy. With our overhaul and recycling process of electric vehicle parts, we are making a significant contribution to a more sustainable future.
“We are convinced that the future of the automotive industry is circular. That is why we’re proud partners of Circle Economy” – Thijs Jasink, COO ACTRONICS Group
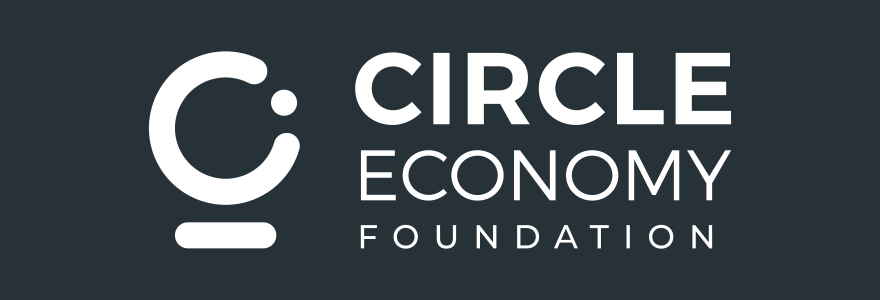